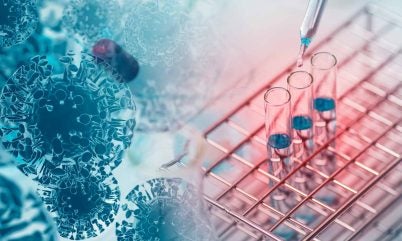
Indena offers custom development services by leveraging the expertise of a specialised team that’s devoted to designing and developing processes and analytical methods.
Thanks to more than 100 years of experience in the field of delivering complex APIs, the company is also committed to reaching each client’s development milestones for botanical, synthetic and microbial fermentation projects. Its collaboration model is based on mutual commitment, trust and upholding the highest standards. Indena provides bespoke services that meet its partners’ specific timelines for the launch and future commercial production of their products.
With time, the company has developed an impressive level of expertise when it comes to handling molecules requiring containment; capitalising on this heritage, the company has implemented state-of-the-art containment solutions for highly potent new chemical entity (NCE) production, which also includes molecules obtained from synthesis-based or fermentation processes. That’s why, because of its custom development and manufacturing organisation (CDMO) services, Indena is the ideal partner for biotech and large/midsize pharma companies interested in these innovative technologies.
What Indena learned from nature
Indena’s first custom development experience dates back to the 1990s and the first oncological blockbuster drug, paclitaxel. The challenge included the development of a sustainable supply chain for the ingredient, designing a method of insulation under high-containment conditions and an analytical control methodology that had to comply with stringent pharmaceutical protocols in terms of purity and stability.
During the development phase, the drug was extracted from the bark of Pacific yew tree in a way that was not sustainable. To make the drug available at commercial scale, the first challenge Indena had to face was to build a robust supply chain for the biomass … which meant implementing its own yew tree cultivations. The second challenge was related to the development of a robust industrial-scale method to extract and purify the intermediate: 10-deacetylbaccatin III. The third problem involved the creation of a reliable analytical framework for the project that, again, had to comply with rigorous pharmaceutical regulations.
Moreover, Indena also had to develop its own synthetic methods to convert the intermediate (10-deacetylbaccatin III) into the final API. The solution devised by Indena for paclitaxel was an extraordinary result and a totally unique experience: the practice of working with Nature has taught Indena to manage complex molecules — from both an analytical and production perspective — of any origin.
Custom services have been a company focus ever since and, thanks to work done during the last 20 years, they represent one of the Indena’s key strengths. Indena manufactures 12 commercial HPAPIs from many different origins, including synthetic, semisynthetic and fermentation-derived molecules.
This positioning has been achieved thanks to Indena’s capacity to handle HPAPIs with an occupational exposure level (OEL) from 1.00–0.02μg/m3. Other contributing factors are the onsite availability of complementary technologies such as GMP-compliant microbial fermentation/biotransformation, synthesis and extraction capabilities, as well as its qualified and cohesive CDMO team. These are Indena’s major technological pillars when it comes to securing customised solutions for its partners.
Sustainability: a concrete commitment
Another cornerstone of Indena is its commitment to sustainability and business continuity. Climate change is one of the most urgent environmental challenges that people, governments and companies have to face, which makes the responsible use of energy imperative. Indena has always been oriented and committed to reducing fossil fuel consumption and use, saving energy and achieving high levels of energy self-production. Such commitment is mainly achieved as a result of the company’s plant management, starting from its most important site in Settala near Milan in Italy; this is where Indena’s CDMO activities are centred.
At the Settala site, we make smart use of a natural gas cogenerator plant to provide power; operational since 2016, it produces 16,566,000 kilowatt-hours per year (both electric and thermal) and enables a reduction of 1,699 tons of oil (TOE) equivalent, which means a reduction of 2,500 tons of CO2 emissions per year. Another important action for sustainability is the use of renewable energy. Indena is equipping all of its European sites with state-of-the-art photovoltaic panels. The total amount of self-produced renewable energy by 2023 will be 5,013,000 kw hours/year, which is equivalent to a saving of 2,340 tons of CO2.
By the end of 2023, 67% of the energy used by Indena will be self-produced, of which almost 23% will be from renewable sources and 5177 tons of CO2 will be saved. All Indena’s European factories are ISO 14001-certified (Environmental Management System) and compliant with ISO 45001 (Occupational Health and Safety Management System). All we do to ensure sustainability also means that Indena is a reliable partner in terms of business continuity as well.
Indena’s cutting-edge equipment and technological solutions
Chemical synthesis of HPAPIs: Indena currently manufactures 12 commercial HPAPIs, including fully synthetic, semi-synthetic and fermentation-derived molecules. This is now a core competency of the company. Each substance is assigned an OEL and allocated to the proper production line according to the required handling and containment rules.
At the Settala facility, Indena can handle HPAPIs with an OEL from 1 μg/m3 to 20 ng/m3. Indena’s HPAPI lines for CDMO activities include the following:
– within P7: two lines for HPAPIs (glass reactors from 30–60l with chromatography)
– within P10: three lines for HPAPIs (glass reactors from 5–60l with chromatography)
– a 1 kilo lab for clinical and commercial supplies of OEL >150ng/m3 products (20l and 60l glass reactors with chromatography and preparative HPLC)
– a 1 kilo lab for clinical and commercial supplies of OEL >20ng/m3 products (2 x 30l glass reactors with chromatography)
– a 1 kilo lab for clinical and commercial supplies of OEL >20ng/m3 products (25l and 2 x 60l glass reactors)
Fermentation solutions: Indena has a fermentation department to do living cell-based biotransformations. Indena’s expertise includes GMP-compliant microbial fermentation and biotransformation and, thanks to the availability of downstream capacity, contained lines for cytotoxic compounds are also available.
Indena’s multipurpose fermentation plant includes a 150l fermenter, 4 x 1,000l fermenters (two lines, 2 x 1,000l) and 1 x 20,000l fermenter. Lab and pilot-scale fermentation capabilities include 2 x 5l fermenters, 2 x 10l fermenters and 1 x 100l fermenter.
Extraction, isolation and purification solutions: APIs derived from natural sources are part of Indena’s core expertise. The Settala site now counts on more than 90 reactors for this specific activity; 400 m3 of industrial capacity for extraction, isolation, distillation, liquid/liquid separation and crystallisation allows Indena to be a global leader in the natural-origin API landscape.
The company offers:
– capacity from small to large industrial scale (stainless steel reactors from 0.4–12m3)
– total solvent storage capacity of 2,000,000l
– extraction: 20,000 tons of processed biomass per year
– pilot and industrial supercritical CO2 extraction (under GMP conditions).
Particle size engineering: Indena’s plant includes:
– large-scale equipment (ATZ4) that can handle 240kg/day of spray dried (SD) material
– intermediate production scale (ATZ5) for APIs with OELs down to 10μg/m3 (20kg-50kg/day of SD material)
– smaller equipment for higher containment levels (OEL 1μg/m3) is under implementation
Both existing spray dryers work with Class 2 organic solvents and can accommodate excipients/copolymers (for drug product intermediates). Spray drying activities are fully supported by suitable analytical techniques, including PSD, DVS, DSC and XRPD.
Analytical research: The company’s main equipment includes:
– liquid chromatography (H-UPLC/HPLC with detection by UV, DAD, ELSD, CAD, RI, FL,MS, MALS)
– ion chromatography
– gas chromatography (HS and direct injection with detection by FID, MS)
– capillary electrophoresis with UV detection
– mass spectroscopy (LC-MS ion trap, LC-MS ion trap + ORBITRAP, LC-MS triple quadrupole, LC-MS single quadrupole, GC-MS single quadrupole)
– nuclear magnetic resonance: 400MHz NMR + autosampler; 1H, 13C, 31P; benchtop 43MHz NMR; 1H
– solid state (TGA, TG/DTA, DSC, XRPD, hot stage microscopy, dynamic vapour sorption, FTIR-ATR, NIR, particle size analyser
– ancillary equipment
At the beginning of 2024, new HPAPI R&D labs will be ready. In this area, synthetic chemists will handle projects involving highly potent products with OELs down to 20ng/m3 with the necessary support of qualified analysts.